在化工、半导体、新能源等工业领域,流体输送设备面临着强腐蚀、高磨损、高温高压等严苛考验。传统金属泵易被酸碱 “啃食”、被颗粒 “磨穿”,而一种以陶瓷为主材的特种泵正在改写规则 ——陶瓷泵。这种看似 “脆弱” 的陶瓷制品,如何成为工业管道中坚韧的 “心脏”?今天咱们就来拆解它的核心构造与工作奥秘。
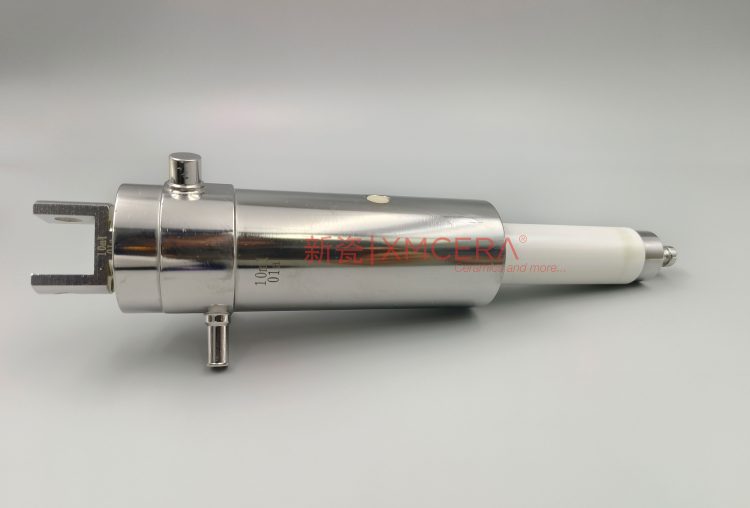
一、颠覆认知的 “瓷骨” 结构:刚柔并济的工业级设计
(1)核心过流部件:陶瓷打造的 “抗蚀铠甲”
-
叶轮与蜗壳:采用 99.7% 高纯氧化铝陶瓷(洛氏硬度 HRA≥85)或碳化硅陶瓷(硬度仅次于金刚石),表面经纳米晶烧结工艺处理,形成光滑致密的保护层。以氧化铝陶瓷叶轮为例,其耐酸碱腐蚀性是 316L 不锈钢的 10 倍以上,在 10% 浓度盐酸中浸泡 30 天重量损失<0.01g。
-
密封环与轴套:采用 “陶瓷对陶瓷” 或 “陶瓷对碳” 的摩擦副组合,配合微米级精度的表面抛光(粗糙度 Ra≤0.1μm),实现低至 0.01mm 的密封间隙,既能防止介质泄漏,又将摩擦系数降至 0.05 以下(普通金属密封副为 0.3-0.5)。
-
传动轴:核心采用高强度氧化锆陶瓷轴(抗弯强度≥800MPa),表面镀覆金刚石涂层,在传递电机扭矩的同时,避免与介质直接接触。某新能源企业实测显示,陶瓷轴的耐磨寿命是不锈钢轴的 8 倍。
-
轴承组件:采用全陶瓷球轴承(氮化硅陶瓷球 + 氧化铝陶瓷套圈),可在 - 200℃~1200℃温度范围内稳定运行,且无需润滑油脂,彻底解决传统轴承的油污污染问题。
-
机械密封:采用波纹管式陶瓷密封环,配合弹簧补偿机构,可自动适应 0.05mm 以内的轴偏移,在压力波动(0-10MPa)时保持密封可靠性。某半导体企业使用案例显示,陶瓷泵的无泄漏运行时间超过 8000 小时。
-
泵体外壳:外层采用球墨铸铁或工程塑料(如 PPS),内部喷涂 500μm 厚度的氧化铝陶瓷涂层,形成 “刚柔复合结构”,既能承受 150℃高温,又可吸收振动能量,噪音比金属泵降低 20dB。
-
核心原理:电机驱动陶瓷叶轮高速旋转(转速 1450-2900rpm),叶片推动流体沿径向甩出,在蜗壳内将动能转化为压力能。由于叶轮和蜗壳表面的陶瓷层具有极低的表面能(水接触角>110°),粘稠介质(如硅胶、树脂)不易粘附,减少堵塞风险。
-
流体优化设计:采用后倾式叶片(角度 25°-35°)和大曲率蜗壳,将水力效率提升至 75% 以上(普通金属泵约 65%),同时降低颗粒介质(如含碳化硅磨料的浆料)对叶片的冲击角度,磨损率减少 40%。
-
隔膜泵结构:采用氧化锆陶瓷隔膜片(厚度 0.3-1mm),通过凸轮机构驱动隔膜往复运动,在泵腔内形成容积变化。陶瓷隔膜的拉伸强度≥300MPa,可承受 10 万次以上往复运动无破裂,在锂电池电解液输送中,实现 ±0.5% 的计量精度。
-
齿轮泵应用:陶瓷齿轮(模数 0.5-2)采用渐开线精密加工,配合 0.02mm 的侧隙设计,在输送高纯度溶剂(如电子级去离子水)时,避免金属离子污染,颗粒截留能力达 5μm 以下。
在钛白粉生产线上,需输送含 30% 硫酸、温度 80℃的酸性浆料。传统氟塑料泵平均 2 个月就因叶轮腐蚀穿孔,而采用碳化硅陶瓷叶轮的泵体,连续运行 18 个月后磨损量<0.3mm,维护成本降低 60%。某磷肥企业使用陶瓷泵输送湿法磷酸(含 3% 固体颗粒),寿命比金属泵提升 3 倍。
(2)半导体制造:纳米级纯净度的守护者
在芯片制造的光刻胶输送环节,要求介质接触部件不含金属离子(钠钾离子<1ppb)。陶瓷泵的全陶瓷流道(氧化铝纯度 99.99%)经 1200℃高温烧结后,杂质析出量低于检测限,配合 0.2μm 的终端过滤器,实现 “零金属污染” 输送,满足 12 英寸晶圆制造的严苛要求。
(3)新能源材料:高粘度介质的征服者
在锂电池正极材料生产中,需输送固含量 60% 的磷酸铁锂浆料(粘度>5000cP)。陶瓷螺杆泵采用双螺杆结构(陶瓷螺杆 + 碳化钨衬套),通过 3D 打印成型的螺旋曲面,将输送效率提升至 90%,且螺杆磨损率每月<0.05mm,远优于金属螺杆的 1mm / 月磨损速度。
四、技术瓶颈与破局之路(1)当前挑战
-
脆性难题:虽然陶瓷硬度高,但抗冲击韧性(KIC=3-5MPa・m½)仍低于金属,在介质中混入大颗粒(>5mm)时易发生叶轮崩裂。
-
加工精度:陶瓷部件需经精密研磨(平面度≤5μm),加工成本是金属部件的 3-5 倍,制约了中低端市场应用。
-
纳米复合技术:在氧化铝中添加 5% 氧化锆(相变增韧),可将断裂韧性提升至 8MPa・m½,抗冲击能力提高 2 倍。
-
增材制造:采用光固化 3D 打印陶瓷坯体,经脱脂烧结后直接成型复杂流道(如双螺旋叶轮),加工周期从传统的 15 天缩短至 3 天。
随着工业 4.0 推进,陶瓷泵正融入智能监测系统:内置的陶瓷压力传感器(精度 ±0.1% FS)实时反馈泵腔压力,温度传感器(误差 ±1℃)监测轴承温度,通过物联网模块实现故障预判。某化工企业试点显示,智能陶瓷泵的停机率降低 40%,运维效率提升 30%。